The industrialization process
Launching your product: a complex and demanding journey
Turning an idea into a manufactured product is a process far more complex than it seems. Each step, from concept to mass production, requires specific resources and a significant investment of time and funding. Indeed, each phase of the project demands different expertise, which is often challenging to gather simultaneously within a company. This is where VF Engineering comes in: we provide you with the right resource, at the right time, according to your needs, and on demand.
The exponential cost of iterations
As the project progresses toward production, the cost of adjustments and modifications increases exponentially. A simple foam mock-up may cost 200 CHF, a quick prototype 1,000 CHF, while a tooling change at the production stage can reach up to 50,000 CHF and result in delays of several weeks or even months. Therefore, it is essential to master each step and manage unforeseen project challenges as effectively as possible..
Every project is unique
In reality, no project follows a perfect linear pattern. Numerous factors come into play, such as certifications, adherence to cost targets, intellectual property protection, technical challenges, geopolitical aspects, and ethical considerations. Each project requires ongoing adaptation and constant adjustment to these variables, and at VF Engineering, we understand these unique challenges..
Our goal: To simplify the industrialization process for you
Initially, our priority is to quickly bring you to a usable result, such as a Minimum Viable Product (MVP). This MVP can be sold to generate revenue and gather user feedback. These valuable insights allow for adjustments and improvements to the product before investing in costly stages.
In the second phase, we finalize the design for mass production. The goal is to ensure that the product can be manufactured using industrial production techniques, such as injection molding. We set up the entire production and logistics chain, including supplier management, assembly, quality control, and packaging, to ensure that each step is controlled and tailored to your needs.
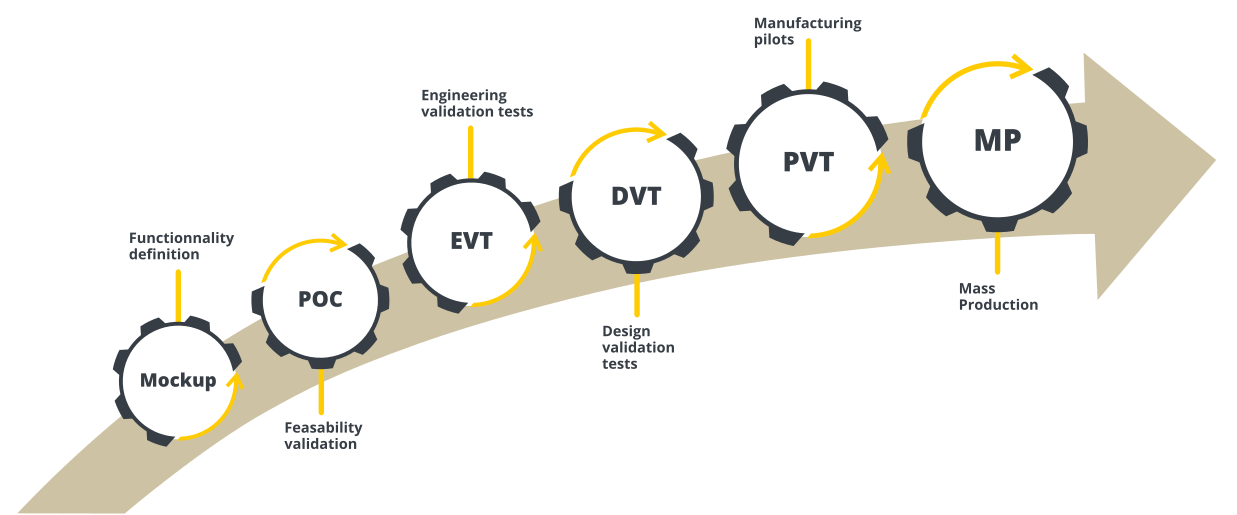
Mockup
The purpose of the mock-up is to visualize the overall appearance of the product, discuss dimensions, materials, and ergonomics, without entering the phase of technical testing. The mock-up is a visual or physical representation of the final product but without functionality. It is common to create several drawings or mock-ups made of paper, cardboard, or foam.
It is generally very difficult to secure funding at this stage.
It took 80 foam models to develop the shape of the first ergonomic computer mouse for Microsoft in 1987.
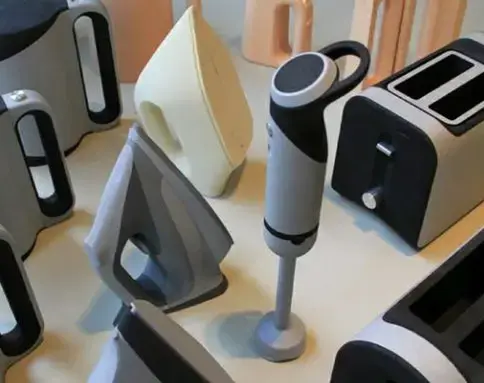
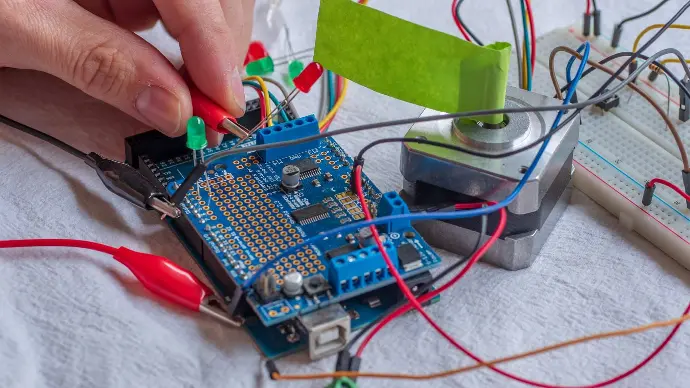
POC (Proof of concept)
The goal of the prototyping phase is to create a technical prototype that functions and resembles the final product, while validating that the technology used meets the customer's needs, that the product is manufacturable, and that it will operate as intended. This stage also serves to finalize the specifications. We try to use as many existing components on the market as possible (e.g., RPI, Arduino, motors, etc.). It is common not to have any mechanical casing at all.
Generally, funding is obtained through 'mini Grants' (<10kCHF), incubators, FFF or crowdfunding.
It took 5,127 prototypes and 15 years to develop the first Dyson cyclone technology vacuum cleaner.
EVT (Engineering Validation Tests)
The goal is to create a demonstrator (MVP) with all the desired technical performances. This prototype is made with components similar to those planned for production and is used to validate the integration of the different parts. It is utilized for laboratory testing (power, thermal, EMI, etc.) but can also be placed in the hands of early users to gather as much field feedback as possible.
At this stage, the product may still have aesthetic limitations. The prototypes created during the EVT phase may appear somewhat 'rough' with a less refined visual aspect: some non-essential elements, such as handles, curves on the casing, or finishes like paint, may still be missing. However, it's important to start considering the industrialization of the product to maximize cost savings and save time in the upcoming phases.
Generally, funding is obtained through Business Angels (BA), Grants (Venturekick, Innosuisse, FIT, ...) or through initial sales.
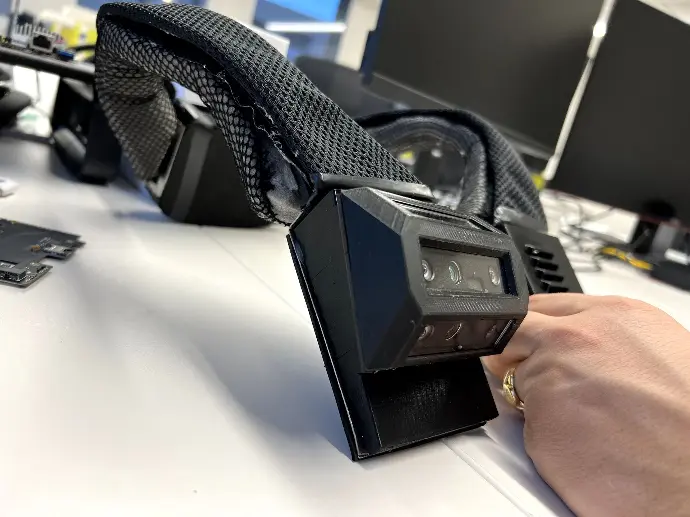
DVT (Design Validation Tests)
While optimizing it for mass production. We implement DFM (Design for Manufacturing), select the final suppliers, and refine the electronic circuits and designs to ensure compliance with all standards and constraints (drops, aging, biocompatibility, FDA, UL, CE, IP, etc.). We also seek to reduce costs (e.g., by decreasing the number of screws, choosing materials, selecting suppliers). Then we design, test, and validate the packaging.
At the end of the DVT, we obtain a series of functional prototypes ready for mass production, accompanied by the bill of materials (BOM) and design documentation. The packaging is often adjusted to optimize palletization.
At this stage, funding typically comes from initial sales of prototypes/MVPs, as well as from Venture Capital (VC) or Corporate VC.
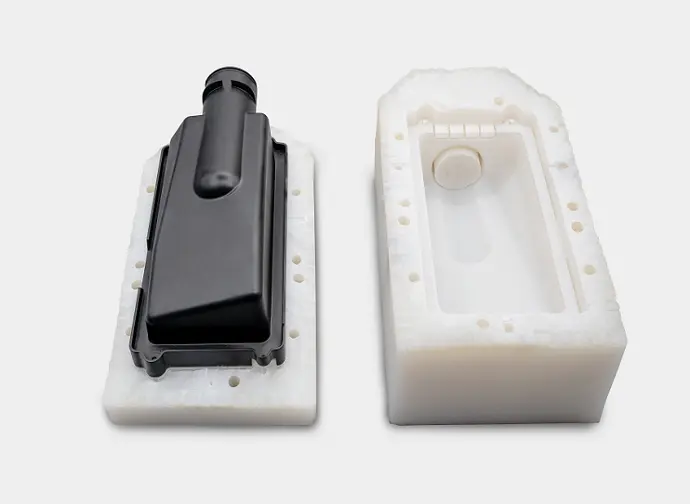
PVT (Production Validation Tests)
This is the final step before mass production. At this stage, the design is finalized, the final tooling is purchased, and the first units are produced for real-world testing (~5% of the planned production). The goal is to validate and optimize the production and assembly lines to reduce costs and ensure repeatable and stable production. Quality controls (QC) are implemented, and any remaining potential risks, such as sourcing from a single supplier, are identified. Additionally, the entire logistics aspect (warehouse, transportation, etc.) must be planned.
Funding at this stage typically comes from pre-sales and bank loans to support mass production.
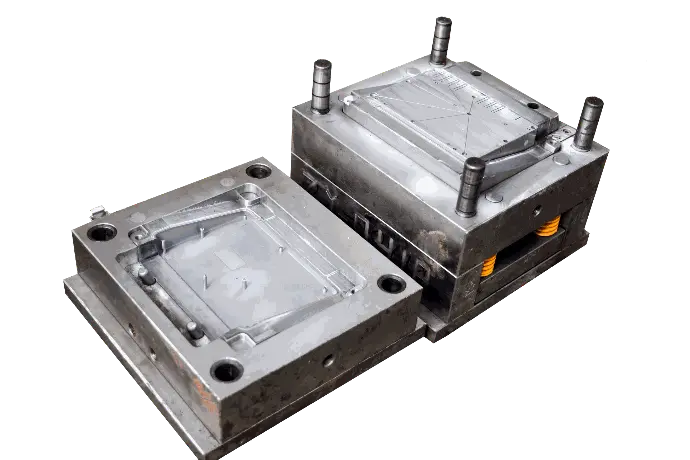
MP (Mass Production)
Finally, your product is 'stable,' and the initial production line can be replicated. We continue to perform all quality controls (QC) as well as a thorough analysis of issues and yield on a small percentage of units to ensure consistent quality and identify any residual problems. Supervision of factories and suppliers is essential to avoid any unforeseen changes (tooling, production parameters, personnel) that could lead to quality variations. We also take advantage of this phase to secure your critical suppliers and optimize costs by seeking every cent of savings on the smallest details, making the production process as efficient as possible.
The primary source of revenue is finally the sale of your product.
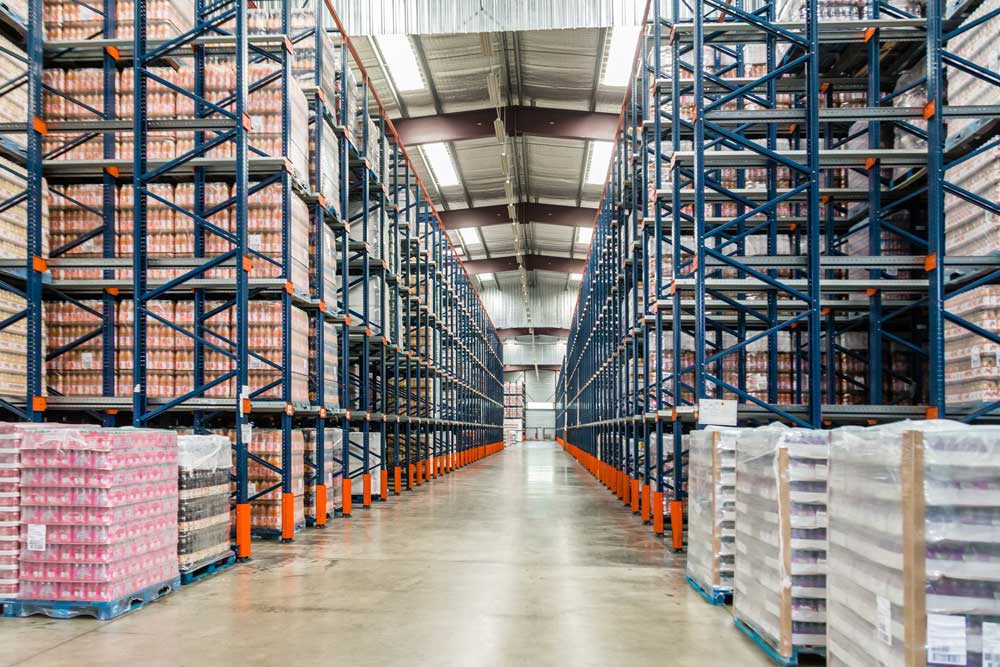
Concrete example: an electric toothbrush
A first mock-up of the electric toothbrush is created, without any functionality. This model, 3D printed or handmade, allows for visualization of the shape, ergonomics, and overall design. At this stage, the goal is to discuss appearance, weight, grip, and dimensions, without concerning ourselves with the internal components. This is a purely aesthetic and ergonomic step where decisions like the shape of the handle, the size of the head, or the choice of colors are made.
We assemble a simple electronic circuit with a motor to make the brush head vibrate or rotate. This is not yet the final version of the product, but an initial proof that the technology works: the motor moves the bristles, and the brush is powered by a battery. The design and materials are not optimized, but the key is to validate that the concept is feasible.
A first functional prototype is created, using components similar to those that will be used in the final version (motor, battery, casing). Technical tests are conducted to validate the interaction between the different parts: the battery charges correctly, the motor operates at the correct power, and the switch responds as expected. Engineers also check for water resistance, the temperature of the motor, and whether the vibrations comply with the specifications.
We ensure that the toothbrush is not only functional but also meets the requirements for design, safety, and performance. Tests focus on battery life, the durability of the casing, and resistance to impacts and moisture. Checks are also carried out to ensure that the toothbrush complies with electrical safety standards. If everything is validated, the final design is finalized.
A first batch is produced on the manufacturing lines that will be used for mass production. We check the stability of the manufacturing processes to ensure that production is repeatable and that quality remains consistent. This stage also allows us to optimize production times and ensure that each product meets the same quality standards.
Mass production begins, with thousands or millions of toothbrushes manufactured, ready to be distributed and marketed. The manufacturing processes are now optimized, ensuring low and controlled production costs along with consistent quality. The logistics chain is established with warehouses in strategic locations, also aimed at optimizing cash flows and VAT (e.g., tax representation).